Dive Brief:
- Multifamily giant Greystar — ranked No. 1 on the NMHC Top 25 Developers list for many years running — broke ground in August on its first U.S. modular housing project. Ltd. Spring Run, located northwest of Pittsburgh in Coraopolis, Pennsylvania, will be made entirely out of modules fabricated at the company’s Modern Living Solutions factory in Knox, Pennsylvania, according to a release.
- The 312-unit property is the third in the Ltd. by Greystar brand, an attainable housing format that caps annual rent increases at either 3% or the trailing 12-month increase in the Consumer Price Index, whichever is greater. Starting with Ltd. Spring Run, the Ltd. brand will work in tandem with the MLS factory to create prefabricated housing modules for its projects.
- Next off the production line after Ltd. Spring Run will be Ltd. Chesapeake Club, which will consist of 224 units in the town of North East, Maryland, according to Andy Mest, MLS managing director. Two more Maryland projects, one in Elkton and one in Southfields, will add a total of 528 units to the Ltd. portfolio. In all, the developer expects to add 1,600 new units over the next 18 months.
Dive Insight:
Built with over 880 prefabricated modules, Ltd. Spring Run will be spread across six residential buildings on a 24-acre lot, according to Mest. The units will be nearly complete when they arrive on site; site work will include utilities, slab preparation and exterior finishing.
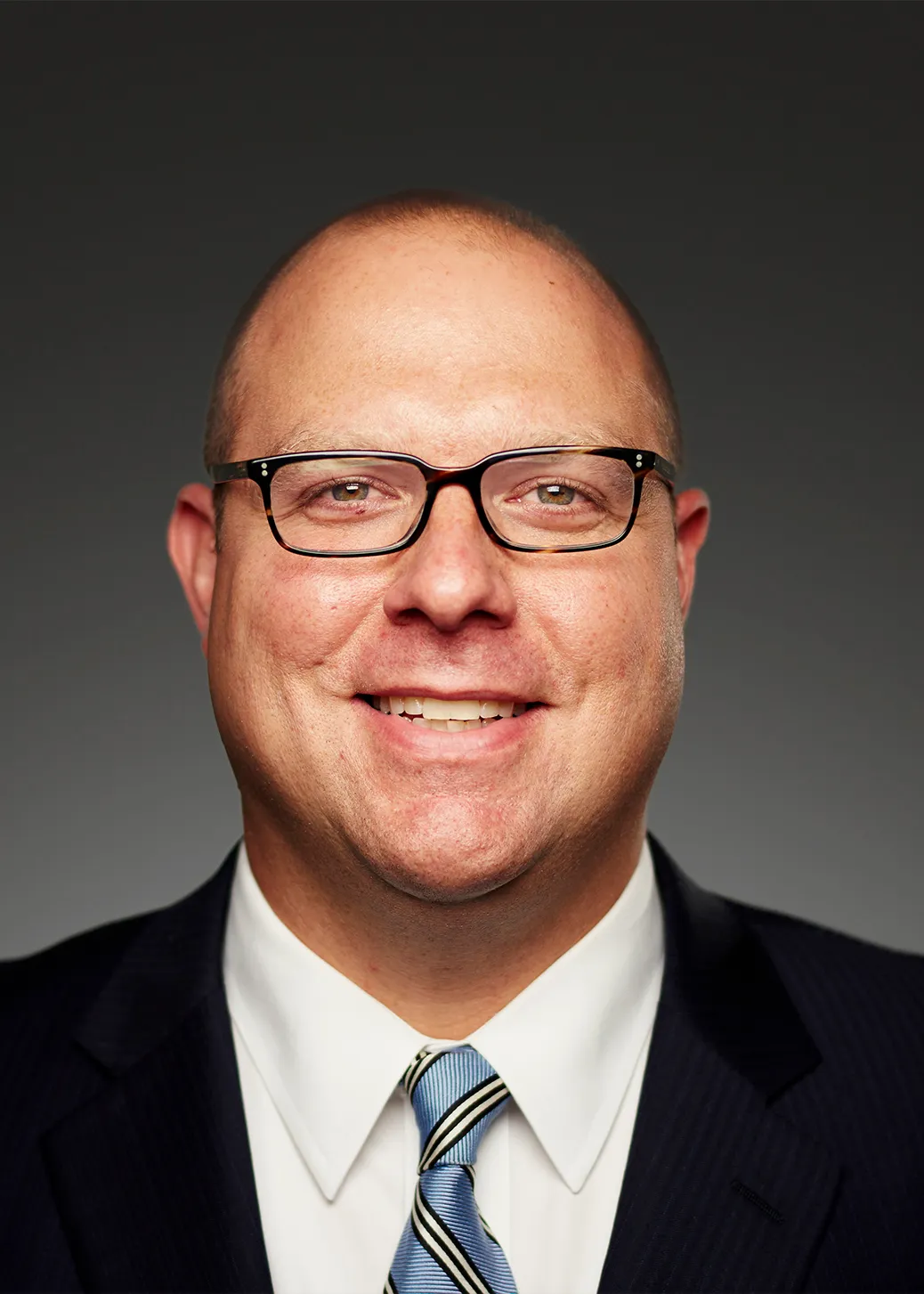
“Everything [made] inside the unit line is about 98% complete. The exterior of the building is watertight, windows are installed, but no facade is installed at the factory,” Mest told Multifamily Dive. “The corridors are essentially left unfinished from the factory perspective, [including] flooring and the connections that need to occur.”
Mest oversaw the production of Greystar’s first modular projects in the U.K. between 2015 and 2018, including the two tallest modular residential structures in the world, standing 38 and 44 stories tall at the 10 Degrees development in London, according to Mest.
Greystar built on this experience to launch its modular operations in the U.S.
“Looking at how we're building in the U.S. and bringing in the lessons we learned over in the U.K. is really where the business idea came about,” Mest told Multifamily Dive. “We're still in the midst of building [Ltd. Spring Run], but to date, everything has gone very, very well. We're about 10% complete today on the project at the factory, and we're preparing the first slab for those units to be set.”
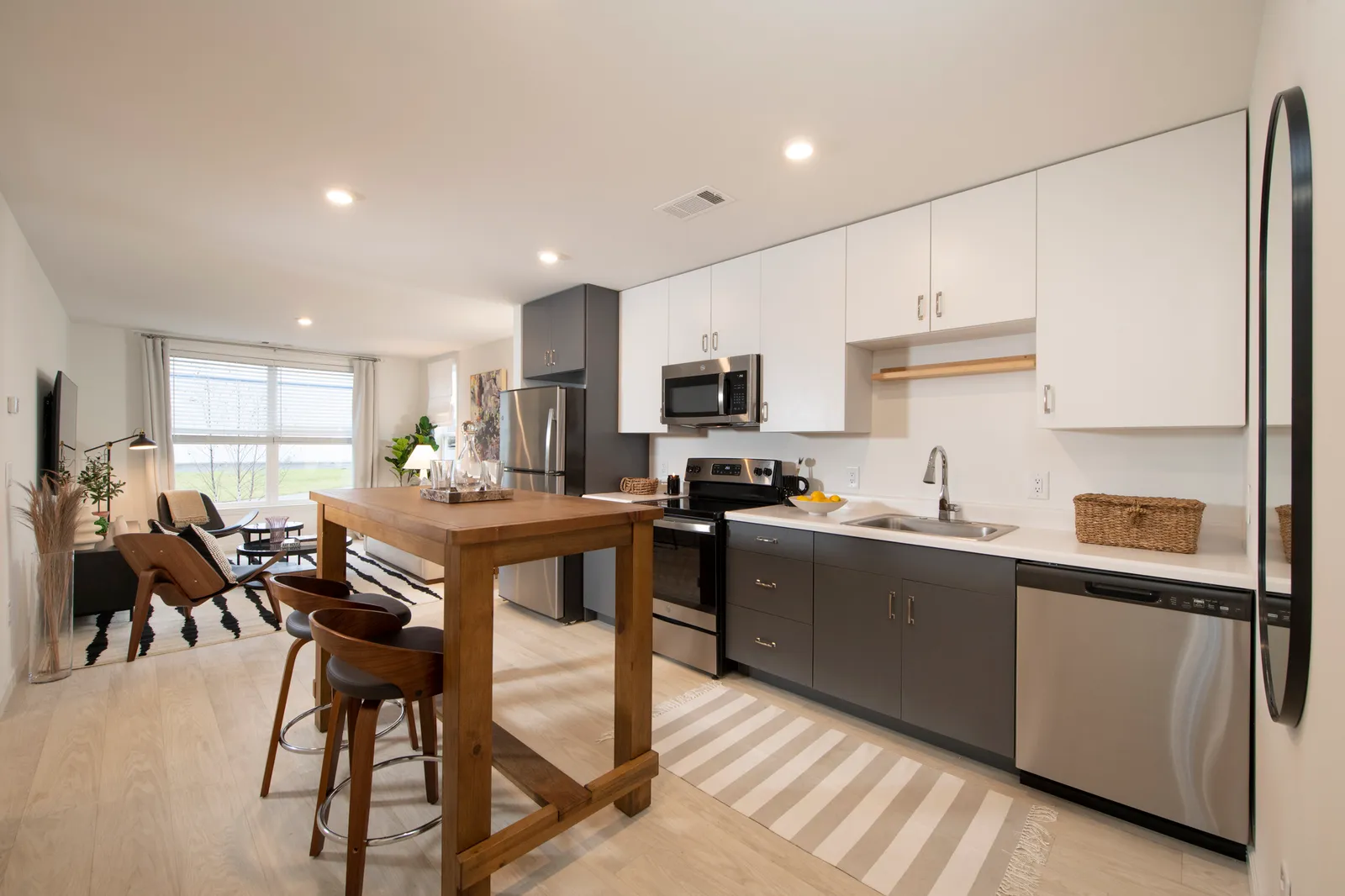
While Ltd. Spring Run’s modules will take an estimated 12 months to fabricate, Mest expects to scale up production at the MLS factory to the point where fabrication time is cut down by 75% on the next project. “We're in the ramp-up stage of our factories,” Mest said. “We've learned a lot from others' misfortune, in terms of trying to hire too quickly.”
The first two Ltd. by Greystar properties — Ltd. Med Center in Houston and Ltd. Champions Ridge in Davenport, Florida — are both site-built projects that opened for move-ins earlier this year. Ltd. Spring Run’s first units are expected in June 2024, according to the release.
While MLS is currently focusing its modular manufacturing efforts on the Mid-Atlantic, Greystar is looking to open new factories across the country in the future.
“It's potentially on the roadmap,” said Mest. “We're laser focused on getting our first factory off the ground and being successful. But our goal would be to be able to serve the larger Greystar geographic footprint we currently have today that is being traditionally built with our modular solution.”
Correction: The name of Greystar’s modular factory is Modern Living Solutions.