Sydney, Australia-based global developer and contractor Lendlease has finished construction on an 80-story luxury residential building in Manhattan’s Midtown East that has been in progress since 2018.
The first move-ins at Sutton Tower’s 120 for-sale units — luxury condos that start around $2.5 million — are scheduled for this summer, the contractor announced last month. Amenities include a swimming pool, gym, spa, screening room, private dining areas and a 1,300-square-foot sculpture garden, according to a release. Gamma Real Estate and JVP Management, both based in New York City, are the developers of the project.
Constructing the 850-foot tower on a 6,000-square-foot jobsite in a dense, urban environment wasn’t without challenges, said Mark Lubrano, senior vice president and project executive for New York construction at Lendlease.
Here, Lubrano speaks with Construction Dive about the delays brought on by the COVID-19 pandemic and the challenge of building up without much wiggle room.
The following has been edited for brevity and clarity.
CONSTRUCTION DIVE: How much coordination has to go into a project like this in Midtown Manhattan?
Mark Lubrano: Any time you are working on a smaller site, there is an extra level of coordination around logistics like deliveries and scheduling — and that is compounded in a dense urban neighborhood like this one. Besides considerations to minimize impact on neighbors, you are also working with limitations regarding site access.
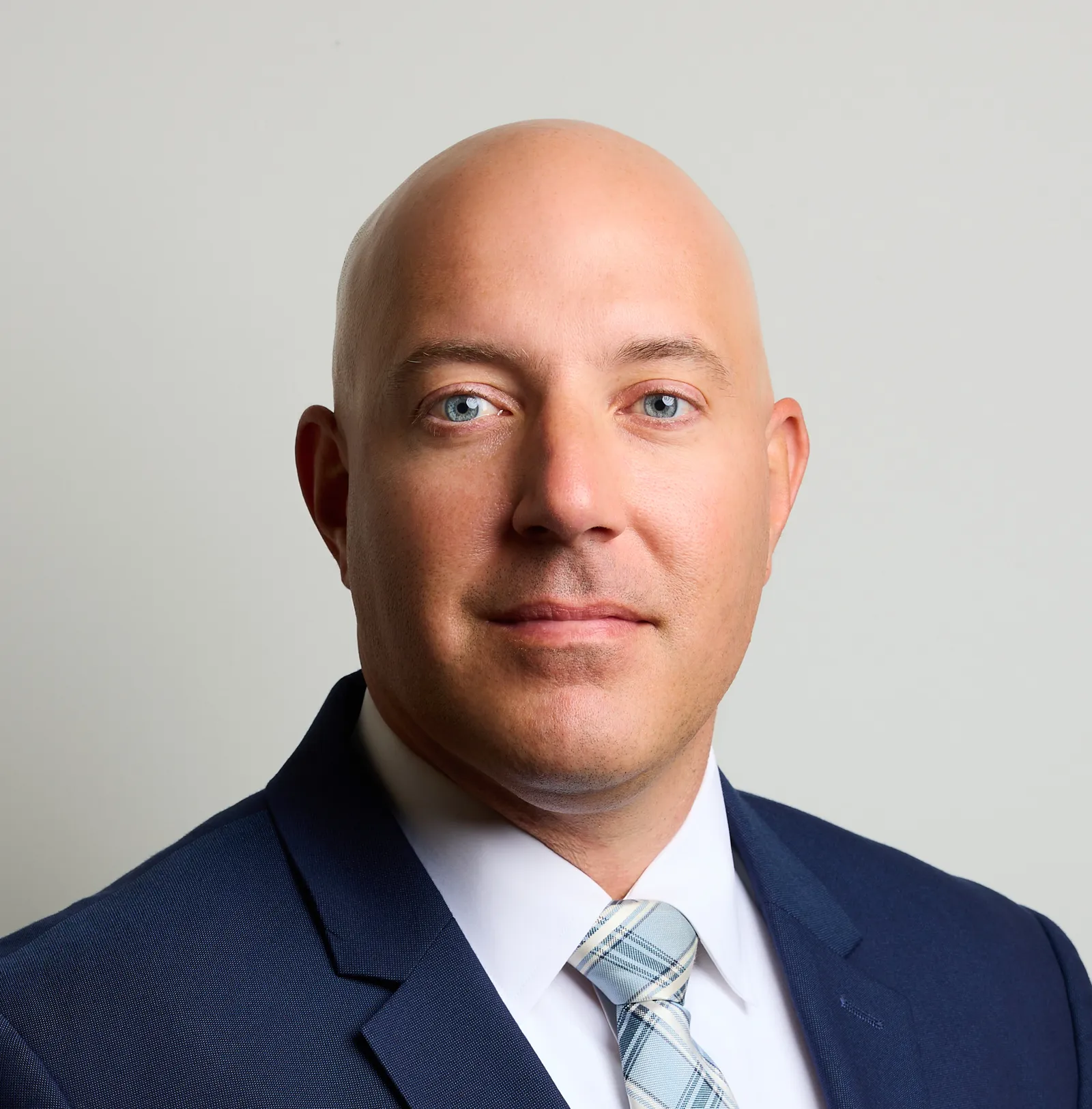
In the case of Sutton Tower, there was not much frontage available to us on 58th Street, other than the parking lane and the first driving lane to be used as lay-down areas. Because of this, we loaded the project from the ground floor, with trucks driving onto the site and unloading in what eventually became the building’s lobby.
This also allowed access to the exterior hoist, which was installed on the backside. Once we completed vertical construction and the hoist came down, we finished the lobby out with the rest of the interiors.
In addition to noise and environmental considerations, there are sometimes physical constraints posed by neighboring buildings when you’re working on a tight, infill site. A solution to this was Sutton Tower’s 10-foot cantilever over the adjacent structures, starting on the 6th floor. We had to work closely with neighboring properties to coordinate the cantilever installation.
Sutton Tower broke ground in 2018. How was it impacted by the pandemic?
Like every other construction project in Manhattan at the time, we shut down for just over two months, beginning in late March 2020. We lost some time installing the exterior curtain wall on the top third of the building, but we were able to recoup that time on the backend of the project.
Fortunately, we were already at a point in construction where most materials and equipment were “stacked and packed,” so we were not impacted by the supply chain delays caused by the pandemic.
Is there anything you learned from this project that you’d use to improve future projects?
Sutton Tower illustrates some of the special considerations that go into an ultra-high-end residential project, particularly in terms of material selection and sourcing.
For example, there is elaborate stonework throughout the project’s interiors, so we spent significant time during the planning phase working with the owner and architect on sourcing and production for the specified types of stone, which primarily came from Italy.
The same was true of the specialty millwork that is such an important part of the building’s luxe atmosphere. Planning well in advance for specialty materials has always been a critical aspect of ensuring a project delivers on schedule, and that is even more true today as we continue to experience significant lead times and delivery delays due to ongoing supply chain and production disruptions.
What was your biggest takeaway from this project?
The biggest takeaway for this project was overcoming the challenges presented by the limited footprint. This included installation of temporary steel decking so that workers could safely access the underside of the 10-foot cantilevers, not to mention using the future lobby space as a loading dock. Small sites can often lead to big issues, but leveraging our expertise gained from the completion of many projects in New York City, we were able to overcome them at Sutton Tower.