Orange, California-based architectural firm AO — formerly known as Architects Orange — has operated a dedicated modular studio since 2016.
A majority of AO’s projects come through two modular factories — Autovol in Nampa, Idaho, and Volumetric Building Cos. in Tracy, California. The architect currently has 11,000 modular units in its pipeline; more than 6,500 of these units are in California, and many of them are affordable housing.
Its ongoing modular projects include The Courtyards on International, a 140-unit affordable development in Oakland, California, designed for Eagle, Idaho-based The Pacific Cos., and Orbisonia Heights in Bay Point, California, a 169-unit affordable property and 22,000-square-foot library designed for Reno, Nevada-based Pacific West Cos.
The group’s approach to its modular projects emphasizes the importance of partnerships and relationships at every stage, according to Ioanna Magiati, partner at AO. Here, Magiati talks with Multifamily Dive about the modular design process, meeting the challenges of developing in California and the firm’s plans for expanding its reach.
This interview has been edited for brevity and clarity.
MULTIFAMILY DIVE: How does the design process for your modular projects differ from that of traditional projects?
IOANNA MAGIATI: Modular design demands advanced technical expertise and strict adherence to a precise grid system. This ensures that modular units, fabricated off-site in factories, align perfectly during assembly.
Unlike conventional projects, where on-site adjustments are feasible, modular construction demands meticulous pre-planning to ensure factory-fabricated units align seamlessly during transport, craning and assembly.
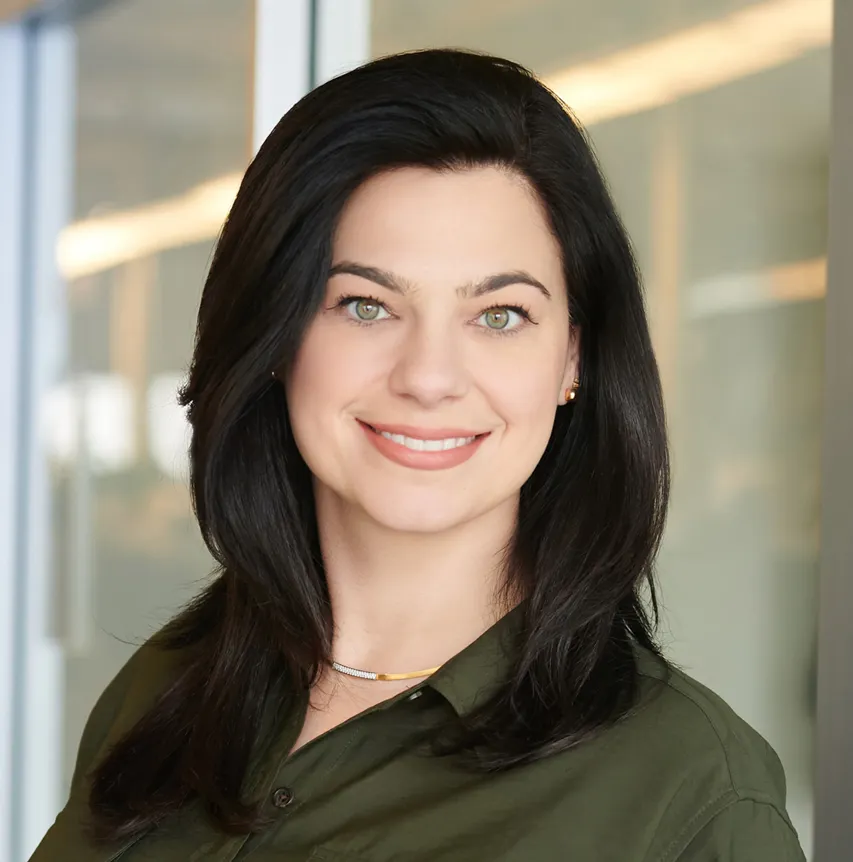
A key distinction is the necessity of close collaboration with the factory from the earliest stages of the design process. This partnership enables the design team to optimize layouts and details to align with the factory’s production capabilities.
Modular units also require additional coordination with specialized consultants and engineers to ensure that every element, from structural systems to mechanical, electrical and plumbing components, integrates seamlessly within the modular framework.
What are some of the benefits of modular design?
The benefits manifest most significantly during the construction phase. Factory-controlled fabrication streamlines production, resulting in faster timelines, reduced labor and material costs and minimized waste. You are able to build your structure above slab or podium in the factory while your foundation or podium in the field is being constructed.
Additionally, factory environments mitigate the risk of weather-related delays, ensuring consistent progress and quality. These efficiencies not only make modular projects cost-effective but also environmentally sustainable, delivering high-quality finished products that meet or exceed traditional construction standards.
While the modular approach may dictate some design constraints, such as unit dimensions and layouts, the finished product is indistinguishable from traditional construction. Modular buildings are designed with the same level of detail, functionality and aesthetic appeal, proving that high efficiency does not compromise design or quality.
Given the difficulty of developing new housing in California, how do modular strategies aid in this process in this state in particular?
Modular construction offers a transformative solution to the challenges of developing new housing in California, including high costs, labor shortages and lengthy timelines. By allowing for parallel construction — fabricating units off-site in factory-controlled environments while site work progresses — modular strategies can reduce project timelines by 30% to 50% and provide greater cost predictability.
This approach also addresses labor shortages by relying on a consistent factory workforce and improves quality control through standardized production processes that meet California’s strict building codes. Additionally, modular construction aligns with the state’s sustainability goals by minimizing waste and reducing environmental impact.
These efficiencies make modular strategies particularly effective for delivering affordable housing, offering a faster, scalable and cost-effective solution to address California’s pressing housing needs.
Do you plan to expand your modular operations into other states?
Currently, AO is focused on delivering affordable modular apartment communities in California, where demand is greatest. However, expanding modular operations to other states depends largely on the proximity of modular factories to project sites. Transportation costs for delivering modules from factories to build sites can be a significant barrier; the farther the distance, the higher the costs, which can make conventional stick-built construction more viable in some cases.
At present, the majority of AO’s modular projects utilize modules from Autovol in Idaho and Volumetric Building Cos. in Tracy, California. This proximity has made Northern California a primary area for our modular developments.
As modular factories continue to be established in more locations nationwide, transporting modules to urban centers across the country will become more feasible, paving the way for modular construction to expand.
While AO has a broad portfolio of projects across the U.S. and globally, we anticipate modular development becoming increasingly prevalent in other states as factory infrastructure grows. We are actively monitoring these developments and are well-positioned to deliver modular solutions wherever they align with project goals and client needs.
Clarification: This story has been updated to indicate that AO works with Autovol and Volumetric Building Cos. on a majority of its modular projects.